by Rachel Young
Background
THE YEAR IS 2040-something . . . Matt Damon is once again stranded on Mars, and this time he wishes to explore more of the planet. He has different modules/sites set up across Mars, but he needs a way to get materials from module to module. This is where the Transport Between Modules 3500 (TBM-3500) comes in.
Design
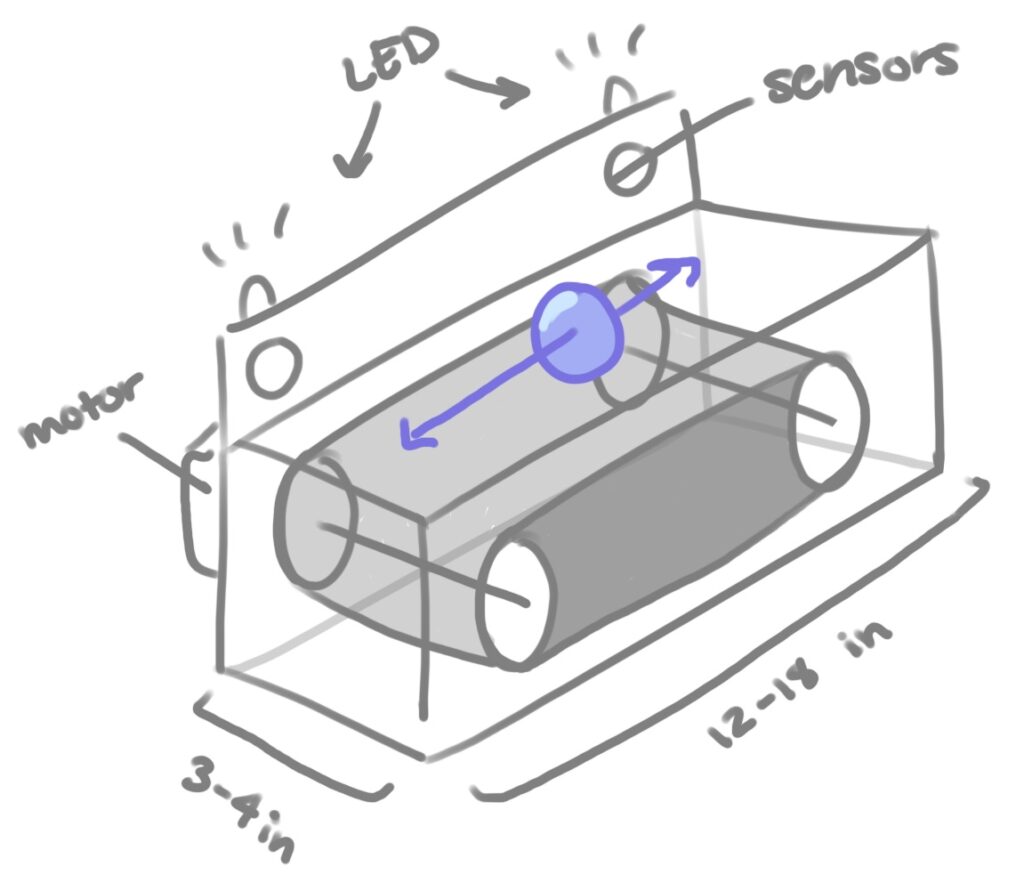
The project essentially acts as a conveyor belt that allows for the transportation of cargo to and from modules in an automated system. Once the cargo arrives at one end, it will be detected via a magnetic sensor and there will be a five second delay to simulate the loading / unloading of cargo. Note: this is more of a scale model as the actual film prop used on set would be much larger and would likely be made out of metal.
Construction
The project is powered by a stepper motor, which is attached to a wheel and axle at one end of the conveyor belt. One of the biggest hurdles of my project was figuring out how to couple the motor to the axle so that it would spin properly. I ended up using a series of terminal wire connectors to connect the axle to the spinning part of the stepper motor.
There is a set of wheels at each end of the box, and instead of using a tread I sewed some velcro onto a piece of canvas and wrapped it around the wheels. In order to make the conveyor belt stay as flat as possible, I had to attach something to the middle of the box to hold up the canvas; this part was actually made out of legos.
There is a magnetic sensor placed at each end of the conveyor belt which senses when the cargo has reached the module. For this project, I used some spare contact sensors for home security systems that react in the presence of a magnetic field.
Final Product
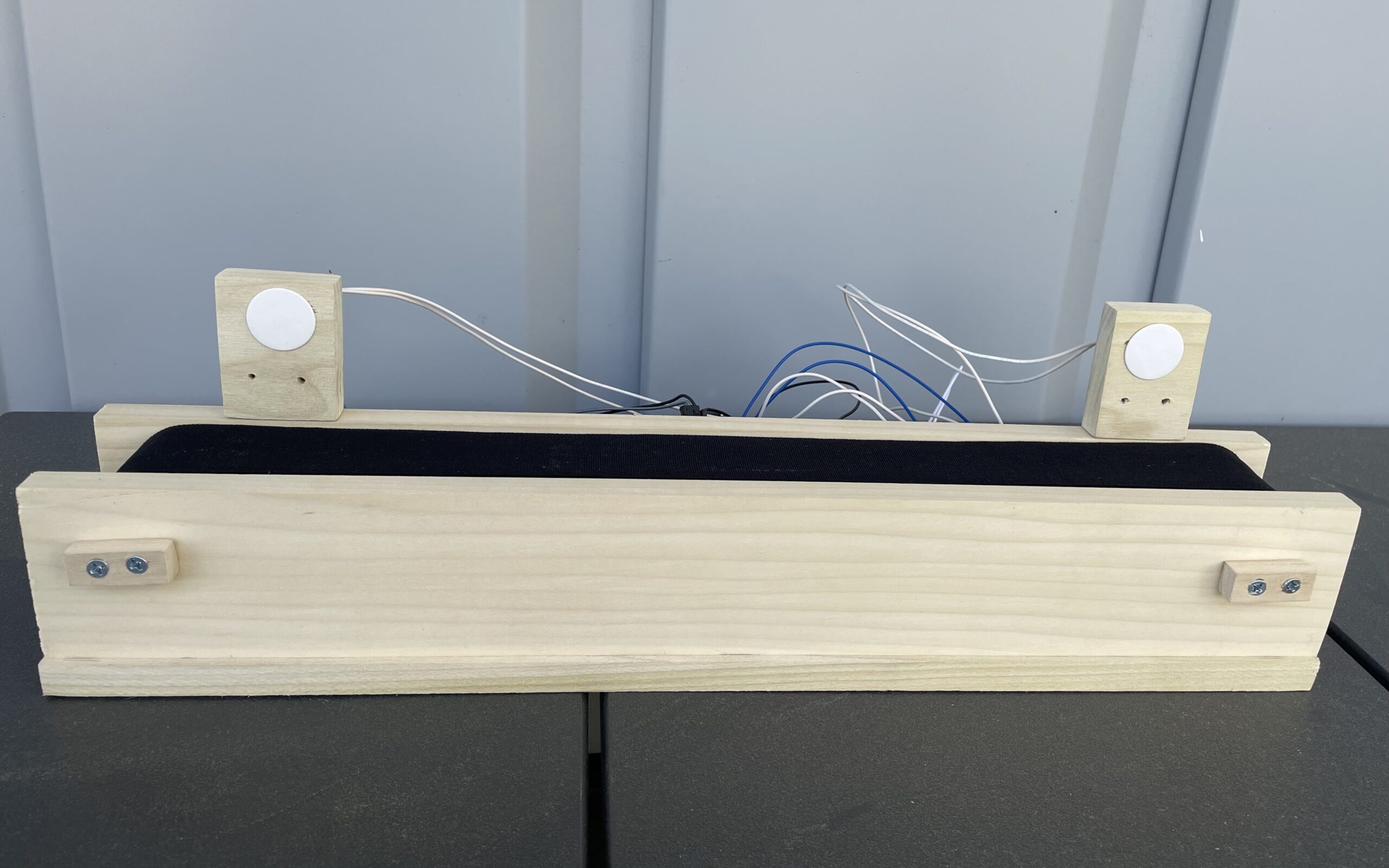
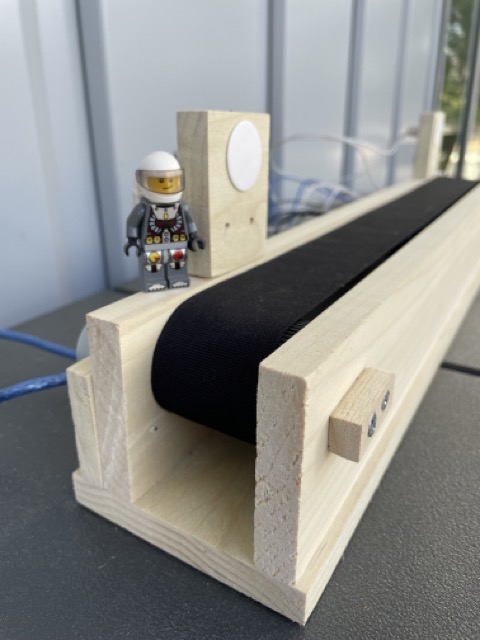
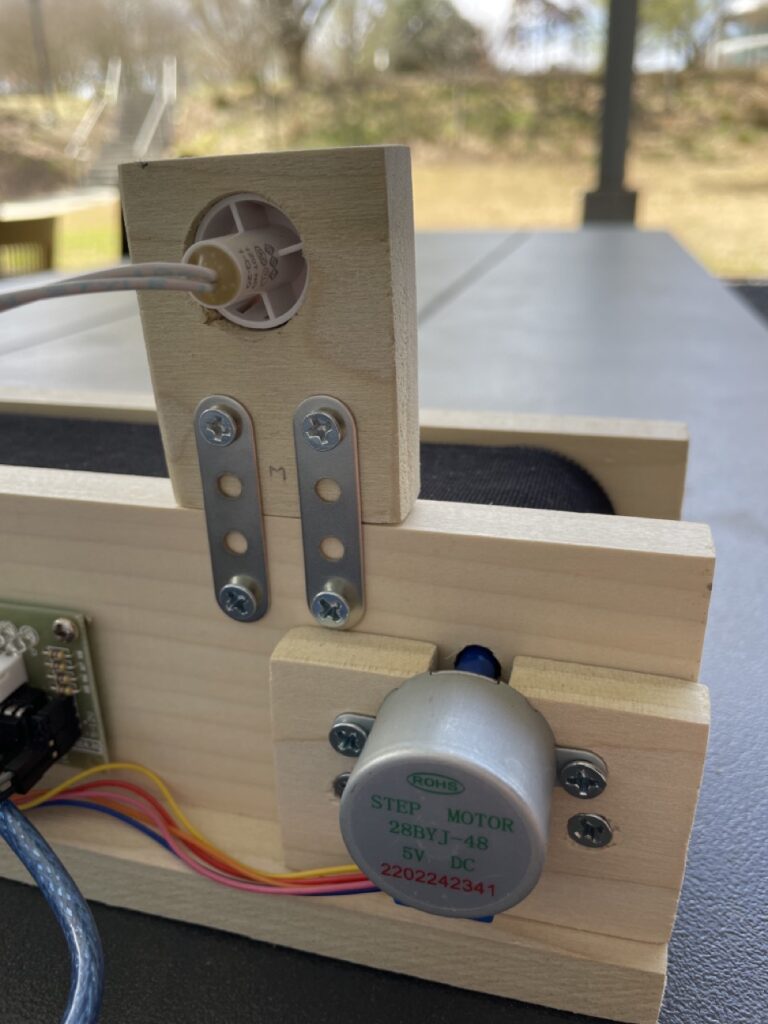
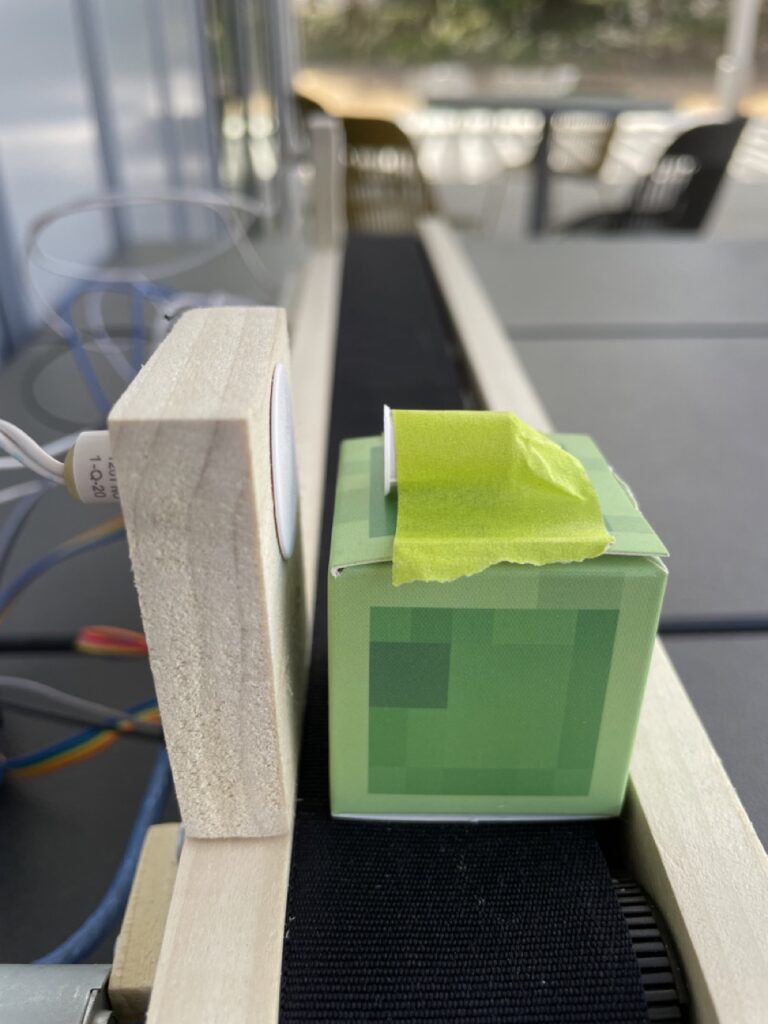
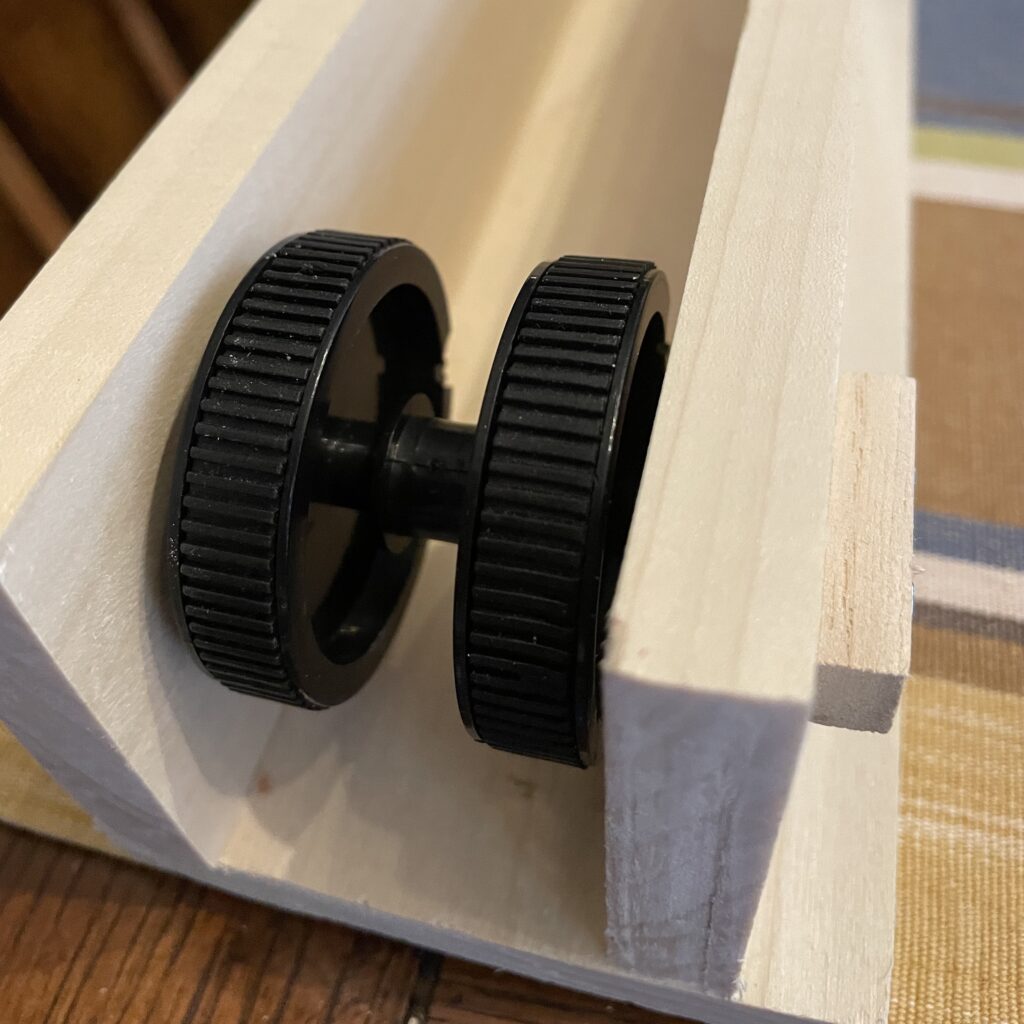
Materials I Used
- Stepper Motor / Stepper Motor Driver Module
- Some Wood and Screws
- Canvas / Fabric (for conveyor belt)
- Contact / Magnetic Sensors (2)
- 1k Ohm Resistors (2)
- Wheel & Axle (2)
- Terminal Wire Connectors
- Various Legos
Schematics
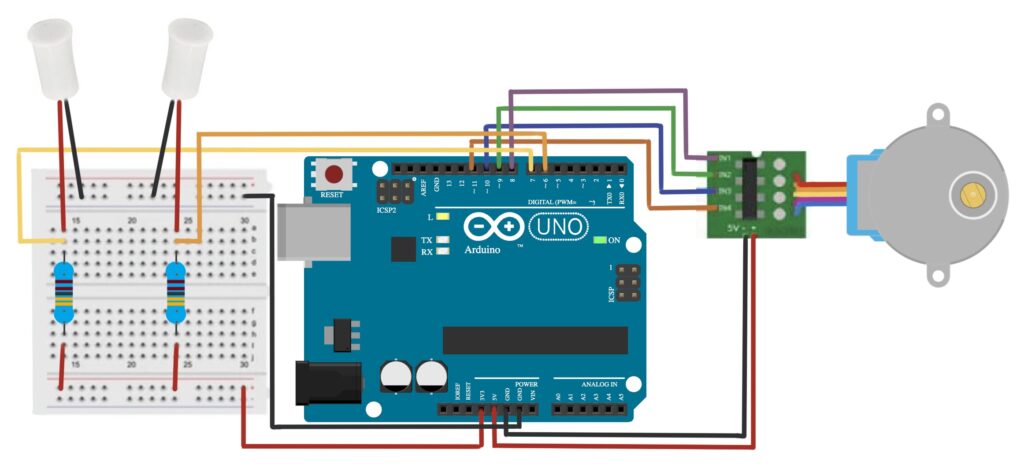
Code
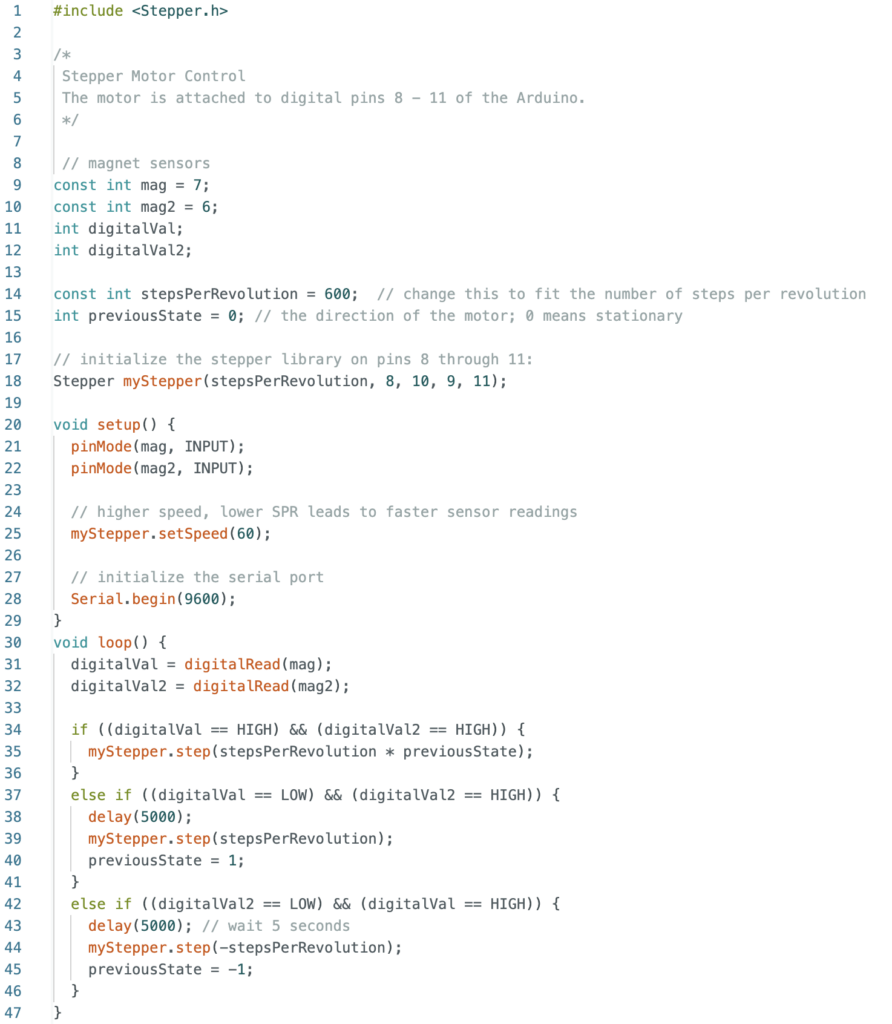
Issues I Had
Getting the sensors to work
I was initially having a lot of trouble getting the sensors to work reliably, so I ended up using an external pull up resistor to force the sensors into a “default” state. Essentially, the voltage was floating between 0 and 5V which was causing the sensor readings to randomly fluctuate between HIGH and LOW. I recommend trying a pull up resistor if you are ever having problems with unreliable digital values. This is the website I referenced.
Powering the motor
I initially hoped to power the motor using the 9V battery, but when I did this I found the motor moved way too slowly. I tried adjusting the values in my code but it was ultimately switching to my laptop’s power that fixed the problem.
Sensor delay
I found when you’re using sensors in tandem with a stepper motor it means sensor readings occur less often. This was obviously a problem for my project because sometimes the sensors would not sense the magnet in time and the cargo would go right off the edge of the conveyor belt. The way I was able to decrease time between sensor readings is by using a higher value for speed and a lower value for steps per revolution for the stepper motor.
Leave a Reply